Advanced Machining in Ancient Egypt Page 5
By Christopher P. Dunn
What follows is a more feasible and logical method and provides an answer to the question of techniques used by the ancient
Egyptians in all aspects of their work.
The fact that the spiral is symmetrical is quite remarkable considering the proposed method of cutting. The taper indicates an
increase in the cutting surface area of the drill as it cut deeper, hence an increase in the resistance. A uniform feed under these
conditions, using manpower, would be impossible.
Petrie theorized that a ton or two of pressure was applied to a tubular drill consisting of bronze inset with jewels. I disagree.
This doesnt take into consideration that under several thousand pounds pressure the jewels would undoubtedly work their
way into the softer substance, leaving the granite relatively unscathed after the attack. Nor does this method explain the
groove being deeper through the quartz.
The method I am about to propose, and hope some of the readers have already figured out, explains how the holes and cores
found at Giza could have been cut. It is capable of creating all the details that Petrie, myself and my colleague puzzled over.
Unfortunately for Petrie, the method was not known at the time he made his studies, so it is not surprising that he could not
find any satisfactory answers.
The application of ultrasonic machining is the only method that completely satisfies logic from a technical viewpoint, and it
explains all noted phenomena. Ultrasonic machining is the oscillatory motion of a tool that chips away material, like a
jackhammer chipping away at a piece of concrete pavement, except much faster and not as measurable in its reciprocation.
The ultrasonic tool-bit, vibrating at 19,000 to 25,000 cycles per second (Hertz) has found unique application in the precision
machining of odd shaped holes in hard, brittle material such as hardened steels, carbides, ceramics and semiconductors. An
abrasive slurry or paste is used to accelerate the cutting action.
The most significant detail of the drilled hole is the groove that is cut deeper through the quartz than the feldspar. Quartz
crystals are employed in the production of ultrasonic sound and, conversely, are responsive to the influence of vibration in the
ultrasonic ranges and can be induced to vibrate at high frequency. In machining granite using ultrasonics, the harder material
(quartz) would not necessarily offer more resistance, as it would during conventional machining practices. An ultrasonically
vibrating tool-bit would find numerous sympathetic partners while cutting through granite, embedded in the granite itself!
Instead of resisting the cutting action, the quartz would be induced to respond and vibrate in sympathy with the high frequency
waves and amplify the abrasive action as the tool cut through it.
The fact that there is a groove may be explained several ways. An uneven flow of energy may have caused the tool to oscillate
more on one side than the other. The tool may have been improperly mounted. A buildup of abrasive on one side of the tool
may have cut the groove as the tool spiraled into the granite.
That the hole and the core have tapered sides is perfectly normal if we consider the basic requirements for all types of cutting
tools. This requirement is that clearance be provided between the tools non-machining surfaces and the workpiece. Instead
of having a straight tube, therefore, we would have a tube with a wall thickness that gradually became thinner along its length.
The outside diameter would gradually get smaller, creating clearance between the tool and the hole, and the inside diameter
would get larger, creating clearance between the tool and the central core. This would allow a free flow of abrasive slurry to
reach the cutting area. It would also explain the tapering of the sides of the hole and the core. Since the tube-drill was a softer
material than the abrasive, the cutting edge would gradually wear away. The dimensions of the hole would correspond to the
dimensions of the tool at the cutting edge. As the tool became worn, the hole and the core would reflect this wear in the form
of a taper.
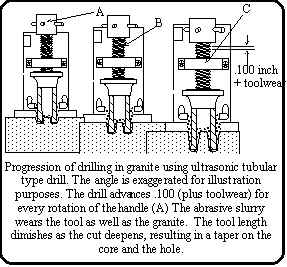
Mechanism For Ultrasonic Drilling.
The spiral groove can be explained if we consider one of the methods that is predominantly used to uniformly advance
machine components. The rotational speed of the drill is not a major factor in this cutting method. The rotation of the drill is
merely a means to advance the drill into the workpiece. Using a screw and nut method the tube drill could be efficiently
advanced into the workpiece by turning the handles (A) in a clockwise direction. The screw (B) would gradually thread
through the nut (C), forcing the oscillating drill into the granite. It would be the ultrasonically induced motion of the drill that
would do the cutting and not the rotation. The latter would only be needed to sustain a cutting action at the workface. By
definition, therefore, the process is not a drilling process, by conventional standards, but a grinding process, in which abrasives
are caused to impact the material in such a way that a controlled amount of material is removed.
The theory of ultrasonic machining resolves all the unanswered questions where other theories have fallen short. Methods may
be proposed that might cover a singular aspect of the machine marks and not progress to the method described here. It is
when we search for a single method that provides an answer for all the data that we move away from primitive and even
conventional machining and are forced to consider methods that are somewhat anomalous for that period in history.
|