Advanced Machining in Ancient Egypt Page 3
By Christopher P. Dunn
Petrie also studied the sawing methods of the pyramid builders. He concluded that their saws must have been at least 9 feet
long. Again, there are indications of modern methods of sawing on the artifacts Petrie was studying. The sarcophagus in the
Kings Chamber inside the Great Pyramid has saw marks on the north end that are identical to saw marks I have seen on
granite surface plates.
Today, these saw marks would reflect either the differences in the aggregate dimensions of a wire band-saw with the abrasive
the wire entraps to do the cutting, or the side-to-side movement of the wire or the wheels that drive the wire. The result of
either of these conditions is a series of slight grooves. The distance between the grooves is determined by the feed-rate and
either the distance between the variation in diameter of the saw, or the diameter of the wheels. The distance between the
grooves on the coffer inside the Kings Chamber is approximately .050 inch.
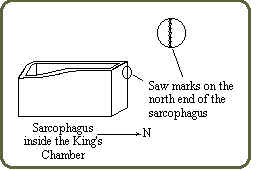
Egyptian artifacts representing tubular drilling are the most clearly astounding and conclusive evidence yet presented to identify
the knowledge and technology existing in pre-history. The ancient pyramid builders used a technique for drilling holes that is
commonly known as "trepanning." This technique leaves a central core and is an efficient means of hole making. For holes that
didnt go all the way through the material, they reached a desired depth and then broke the core out of the hole. It was not
only evident in the holes that Petrie was studying, but on the cores cast aside by the masons who had done the trepanning.
Regarding tool marks which left a spiral groove on a core taken out of a hole drilled into a piece of granite, he wrote:
"The spiral of the cut sinks .100 inch in the circumference of 6 inches, or 1 in 60, a rate of ploughing out of the quartz and
feldspar which is astonishing."
After reading this, I had to agree with Petrie. This was an incredible feed-rate for drilling into any material, let alone granite. I
was completely confounded as to how a drill could achieve this feedrate. Petrie was so astounded by these artifacts that he
attempted to explain them at three different points in one chapter. To an engineer in the 1880s, what Petrie was looking at
was an anomaly. The characteristics of the holes, the cores that came out of them, and the tool marks indicated an
impossibility. Three distinct characteristics of the hole and core make the artifacts extremely remarkable. They are...
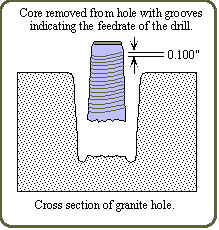
1. A taper on both the hole and the core.
2. A symmetrical helical groove following these tapers which showed that the drill advanced into the granite at a feed rate of
.100 inch per revolution of the drill.
3. The confounding fact that the spiral groove cut deeper through the quartz than through the softer feldspar. In conventional
machining the reverse would be the case.
Mr. Donald Rahn of Rahn Granite Surface Plate Co., Dayton, Ohio, told me, in 1983, that in drilling granite, diamond drills,
rotating at 900 revolutions per minute, penetrate at the rate of 1 inch in 5 minutes. This works out to be .0002 inch per
revolution, meaning that the ancient Egyptians were able to cut their granite with a feed rate that was 500 times greater.
|