Advanced Machining in Ancient Egypt
By Christopher P. Dunn
Egypt. Land of the Pyramids and a vast collection of evidence that, like a taciturn teenager, is begging for understanding.
Contrary to conventional thought, for decades there has been an undercurrent of speculation that the pyramid builders were
more advanced. The speculation is well placed. When attempts have been made to build pyramids using the theorized
methods of the ancient Egyptians, they have fallen considerably short. The great pyramid is 483 feet high and houses 70 ton
pieces of granite lifted to a level of 175 feet. Theorists have struggled with stones weighing up to 2 tons to a height of a few
feet. One wonders if these were attempts to prove that primitive methods are capable of building the Egyptian pyramids or the
opposite? Executing this theory to practice has not revealed the theory to be correct. Do we need to revise the theory, or will
we continue to educate our young with erroneous data?
In August, 1984, I had an article published in Analog magazine entitled "Advanced Machining in Ancient Egypt?" It was a
study of "Pyramids and Temples of Gizeh," the work of Sir. William Flinders Petrie. Since the articles publication, I have
been fortunate to visit Egypt twice. With each visit I leave with more respect for the industry of the ancient pyramid builders.
An industry, by the way, that does not exist today.
While in Egypt in 1986, I visited the Cairo museum and gave a copy of my article, along with a business card, to the director
of the museum. He thanked me kindly, threw it in a drawer to join other sundry material, and turned away. Another
Egyptologist led me to the "tool room" to educate me in the methods of the ancient masons by showing me a few cases that
housed primitive copper tools.
I asked my host about the cutting of granite, for this was the focus of my article. He explained how they cut a slot in the granite
and inserted wooden wedges which they soaked with water. The wood swelled creating pressure that split the rock. Splitting
rock is vastly different than machining it and this did not explain how copper implements were able to cut granite, but he was
so enthusiastic with his dissertation, I did not wish to interrupt.
To prove his argument, he walked me over to a nearby travel agent encouraging me to buy airplane tickets to Aswan, where,
he said, the evidence is clear. I must, he said, see the quarry marks there and the unfinished obelisk. Dutifully, I bought the
tickets and arrived at Aswan the next day. (After learning some of the Egyptian customs, I got the impression that my
Egyptologist friend had made that trip to the travel agent many times.)
The Aswan quarries were educational. The obelisk weighs approximately 3,000 tons.
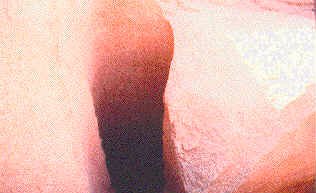
Drill hole at the Aswan Quarries
However, the quarry marks I saw there did not satisfy me as being the only means by which the pyramid builders quarried
their rock. Located in the channel, which runs the length of the obelisk, is a large round hole drilled into the bedrock hillside,
measuring approximately 12 inches in diameter and 3 feet deep. The hole was drilled at an angle with the top intruding into the
channel space. The ancients may have used drills to remove material from the perimeter of the obelisk, knocked out the webs
between the holes and then removed the cusps.
While strolling around the Giza Plateau later in the week, I started to question the quarry marks at Aswan even more. (I also
questioned why the Egyptologist had deemed it necessary to buy an airplane ticket to look at them.) I was to the South of the
second pyramid when I found an abundance of quarry marks of similar nature. The granite casing stones which had sheathed the second pyramid were stripped
off and lying around the base in various stages of destruction. Typical to all of the granite stones worked on were the same
quarry marks that I had seen at Aswan earlier in the week.
This was puzzling to me. Disregarding the impossibility of Egyptologists theories on the ancient pyramid builders quarrying
methods, are they really valid from a non-technical, logical viewpoint? If these quarry marks distinctively identify the people
who created the pyramids, why would they engage in such a tremendous amount of extremely difficult work only to destroy
their work after having completed it? It seems to me that these kinds of quarry marks were from a later period of time and
were created by people who were interested only in obtaining granite, without caring from where they got it.
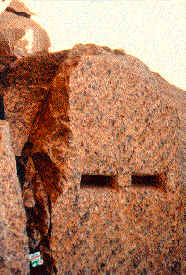
Quarry marks at Aswan
Archeology is largely the study of historys toolmakers. It is with tools and artifacts created with tools, that we come to
understand a societys level of advancement. The hammer is probably the first tool ever invented, and by hammer working
metals, relatively unsophisticated tools have forged some elegant and most beautiful artifacts. Ever since man first learned that he could effect
profound changes in his environment by applying force with a reasonable degree of accuracy, the development of tools has
been a continuous and fascinating aspect of human endeavor.
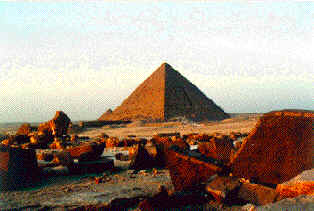
Quarry marks on the Giza Plateau
The Great Pyramid leads a long list of artifacts that have been incredibly misunderstood and misinterpreted by Egyptologists.
They have postulated theories and methods based on a collection of tools that are, at best, questionable. For the most part,
primitive tools that have been uncovered would be considered contempor-aneous with the artifacts of the same period. This
period in Egyptian history, however, resulted in artifacts being produced in prolific number with no tools surviving to explain
their creation. The ancient Egyptians left artifacts behind that are unexplainable in simple terms. The tools that have been
uncovered do not fully represent the "state-of-the-art" that is physically evident in these artifacts. There are some intriguing
objects surviving this civilization which, despite its most visible and impressive monuments, has left us with only a sketchy
understanding of its full experience on planet Earth.
We would be hard pressed to produce many of these artifacts today, even using our advanced methods of manufacturing. The
tools displayed as instruments for the creation of these incredible artifacts are physically incapable of reproducing many of the
artifacts in question. Along with the enormous task of quarrying, cutting and erecting the Great Pyramid and its neighbors,
thousands of tons of hard igneous rock, such as granite and diorite, were carved with extreme proficiency and accuracy. After
standing in awe before these engineering marvels and then being shown a paltry collection of copper implements in the tool
case at the Cairo Museum, one comes away with a sense of frustration, futility and wonder.
The first British Egyptologist, Sir. William Flinders Petrie, recognized that these tools were insufficient. He admitted it in his
book "Pyramids and Temples of Gizeh", and expressed amazement regarding the methods the ancient Egyptians were using to
cut hard igneous rocks, crediting them with methods that "......we are only now coming to understand." So why do modern
Egyptologists identify this work with a few primitive copper instruments?
I am not an Egyptologist. I am a technologist. I do not have much interest in who died when and whom they may have taken
with them, where they went to or when they may be coming back. No lack of respect for the mountain of work and the
millions of hours of study conducted on this subject by highly intelligent scholars (professional and amateur), but my interest,
therefore my focus, is elsewhere. When I look at an artifact with the view of how it was manufactured, I am unencumbered
with a predisposition to filter out possibilities because of historical or chronological inequity. Having spent most of my career
involved with the machinery that actually creates artifacts of the modern kind, such as jet-engine components, I am fairly well
equipped to analyze and determine the methods necessary for recreating an artifact under study. I have been fortunate, also,
to have training and experience in some non-conventional methods of manufacturing, such as laser processing and electrical
discharge machining. That said, I should state that contrary to some popular speculations, I have not seen the work of laser
cutting on the Egyptian rocks. Still, there is evidence of other non-conventional machining methods, along with more
sophisticated, conventional type sawing, lathe and milling practices.
Undoubtedly, some of the artifacts that Petrie was studying were produced using lathes. There is evidence, too, in the Cairo
Museum of clearly defined lathe tool marks on some "sarcophagi" lids. The Cairo Museum contains enough evidence that,
when properly analyzed, will prove beyond all shadow of doubt that the ancient Egyptians used highly sophisticated
manufacturing methods. For generations the focus has centered on the nature of the cutting tools that the ancient Egyptians
used. While in Egypt in February 1995, I uncovered evidence that clearly moves us beyond that question to ask "what guided
the cutting tool?"
Although the ancient Egyptians are not given credit for having a simple wheel, the evidence proves they had a more
sophisticated use for the wheel. The evidence of lathe work is markedly distinct on some artifacts that are housed in the Cairo
Museum and also those that were studied by Petrie. Two pieces of diorite in Petries collection were identified by him to be
the result of true turning on a lathe.
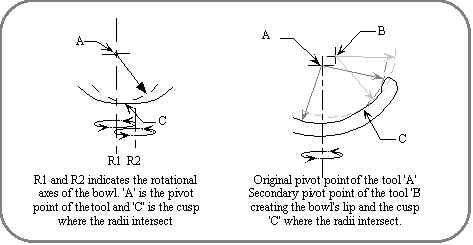
Creating Petries bowl shards.
It is true that intricate objects can be created without the aid of machinery, simply by rubbing the material with an abrasive,
such as sand, using a piece of bone or wood to apply pressure. The relics Petrie was looking at, however, in his words "could
not be produced by any grinding or rubbing process which pressed on the surface."
To the inexperienced eye, the object Petrie was studying would hardly be considered remarkable. It was a simple bowl, made
out of simple rock. Studying the bowl closely, however, Petrie found that the spherical concave radius, forming the dish, had
an unusual feel to it. Closer examination revealed a sharp cusp where two radii intersected. This indicates that the radii were
cut on two separate axes of rotation.
Having worked on lathes, I have witnessed the same condition when a component has been removed from the lathe and then
worked on again without being recentered properly.
On examining other pieces from Giza, Petrie found another bowl shard which had the marks of true lathe-turning. This time,
though, instead of shifting the workpieces axis of rotation, a second radius was cut by shifting the pivot point of the tool. With
this radius they machined just short of the perimeter of the dish, leaving a small lip. Again, a sharp cusp defined the intersection
of the two radii.
While browsing through the Cairo Museum, I found evidence of lathe turning on a large scale. A sarcophagus lid had
distinctive marks of lathe turning.
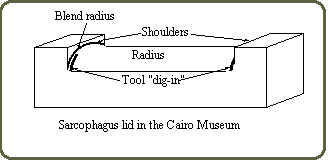
Sarcophagus Lid in the Cairo Museum
The radius of the lid terminated with a blend radius at shoulders on both ends. The tool marks near these corner radii are the same as those I have witnessed when turning
an object with an intermittent cut. The tool is deflected under pressure from the cut. It then relaxes when the section of cut is
finished. When the workpiece comes round again to the tool, the initial pressure causes the tool to dig in. As the cut
progresses, the amount of "dig in" is diminished.
On the sarcophagus lid in the Cairo Museum, tool marks indicating these conditions are exactly where one would expect to
find them!
Petrie also studied the sawing methods of the pyramid builders. He concluded that their saws must have been at least 9 feet
long. Again, there are indications of modern methods of sawing on the artifacts Petrie was studying. The sarcophagus in the
Kings Chamber inside the Great Pyramid has saw marks on the north end that are identical to saw marks I have seen on
granite surface plates.
Today, these saw marks would reflect either the differences in the aggregate dimensions of a wire band-saw with the abrasive
the wire entraps to do the cutting, or the side-to-side movement of the wire or the wheels that drive the wire. The result of
either of these conditions is a series of slight grooves. The distance between the grooves is determined by the feed-rate and
either the distance between the variation in diameter of the saw, or the diameter of the wheels. The distance between the
grooves on the coffer inside the Kings Chamber is approximately .050 inch.
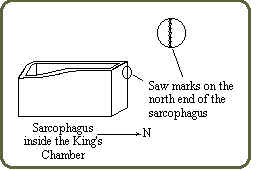
Egyptian artifacts representing tubular drilling are the most clearly astounding and conclusive evidence yet presented to identify
the knowledge and technology existing in pre-history. The ancient pyramid builders used a technique for drilling holes that is
commonly known as "trepanning." This technique leaves a central core and is an efficient means of hole making. For holes that
didnt go all the way through the material, they reached a desired depth and then broke the core out of the hole. It was not
only evident in the holes that Petrie was studying, but on the cores cast aside by the masons who had done the trepanning.
Regarding tool marks which left a spiral groove on a core taken out of a hole drilled into a piece of granite, he wrote:
"The spiral of the cut sinks .100 inch in the circumference of 6 inches, or 1 in 60, a rate of ploughing out of the quartz and
feldspar which is astonishing."
After reading this, I had to agree with Petrie. This was an incredible feed-rate for drilling into any material, let alone granite. I
was completely confounded as to how a drill could achieve this feedrate. Petrie was so astounded by these artifacts that he
attempted to explain them at three different points in one chapter. To an engineer in the 1880s, what Petrie was looking at
was an anomaly. The characteristics of the holes, the cores that came out of them, and the tool marks indicated an
impossibility. Three distinct characteristics of the hole and core make the artifacts extremely remarkable. They are...
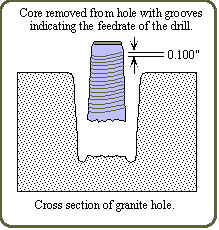
1. A taper on both the hole and the core.
2. A symmetrical helical groove following these tapers which showed that the drill advanced into the granite at a feed rate of
.100 inch per revolution of the drill.
3. The confounding fact that the spiral groove cut deeper through the quartz than through the softer feldspar. In conventional
machining the reverse would be the case.
Mr. Donald Rahn of Rahn Granite Surface Plate Co., Dayton, Ohio, told me, in 1983, that in drilling granite, diamond drills,
rotating at 900 revolutions per minute, penetrate at the rate of 1 inch in 5 minutes. This works out to be .0002 inch per
revolution, meaning that the ancient Egyptians were able to cut their granite with a feed rate that was 500 times greater.
The other characteristics create a problem. They cut a tapered hole with a spiral groove that was cut deeper through the
harder constituent of the granite. If conventional machining methods cannot answer just one of these problems, where do we
look to answer all three? I was just as puzzled as Petrie was when faced with this evidence. When I finally found a solution to
the problem, I could not wait to share it. So I challenged some toolmakers I was working with who had used machine tools
and drills day in and day out for decades. All of them but one gave up on the problem saying it could not be done. Each day I
would ask this one toolmaker if he had come up with a solution. Each day he said he was still working on it. I offered, but he
would not even take a hint! It was a couple of weeks later before he came back to me and said, "You know I think I have the
answer to this problem. But it creates another problem.... They didnt have machinery like that back then!"
He had independently analyzed the characteristics of what Petrie was puzzling over and had come up with the same
conclusion as I had. We had both set out to find a method of manufacturing that would explain all the characteristics found on
these artifacts.
I have discussed descriptions of several artifacts having tool marks and characteristics that identified conventional methods of
machining. A sophisticated use of the lathe is clearly evident on artifacts described by William Flinder Petrie in 1883, where
radii were being cut in diorite. A large sarcophagi lid in the Cairo Museum has distinct tool marks which are common when
turning objects with intermittent cuts on a lathe. The question in my mind is out of what kind of materials were their tools
made? In conventional machining the tool would need to be hard enough to cut one of the hardest materials there is, yet tough
enough not to break under pressure. Their ability to make these cuts without the rock splintering is astounding! (Note: For
those who are locked into the "official" chronology of the development of metals - copper doesnt cut it. It is like saying that
aluminum could be cut with butter.)
What follows is a more feasible and logical method and provides an answer to the question of techniques used by the ancient
Egyptians in all aspects of their work.
The fact that the spiral is symmetrical is quite remarkable considering the proposed method of cutting. The taper indicates an
increase in the cutting surface area of the drill as it cut deeper, hence an increase in the resistance. A uniform feed under these
conditions, using manpower, would be impossible.
Petrie theorized that a ton or two of pressure was applied to a tubular drill consisting of bronze inset with jewels. I disagree.
This doesnt take into consideration that under several thousand pounds pressure the jewels would undoubtedly work their
way into the softer substance, leaving the granite relatively unscathed after the attack. Nor does this method explain the
groove being deeper through the quartz.
The method I am about to propose, and hope some of the readers have already figured out, explains how the holes and cores
found at Giza could have been cut. It is capable of creating all the details that Petrie, myself and my colleague puzzled over.
Unfortunately for Petrie, the method was not known at the time he made his studies, so it is not surprising that he could not
find any satisfactory answers.
The application of ultrasonic machining is the only method that completely satisfies logic from a technical viewpoint, and it
explains all noted phenomena. Ultrasonic machining is the oscillatory motion of a tool that chips away material, like a
jackhammer chipping away at a piece of concrete pavement, except much faster and not as measurable in its reciprocation.
The ultrasonic tool-bit, vibrating at 19,000 to 25,000 cycles per second (Hertz) has found unique application in the precision
machining of odd shaped holes in hard, brittle material such as hardened steels, carbides, ceramics and semiconductors. An
abrasive slurry or paste is used to accelerate the cutting action.
The most significant detail of the drilled hole is the groove that is cut deeper through the quartz than the feldspar. Quartz
crystals are employed in the production of ultrasonic sound and, conversely, are responsive to the influence of vibration in the
ultrasonic ranges and can be induced to vibrate at high frequency. In machining granite using ultrasonics, the harder material
(quartz) would not necessarily offer more resistance, as it would during conventional machining practices. An ultrasonically
vibrating tool-bit would find numerous sympathetic partners while cutting through granite, embedded in the granite itself!
Instead of resisting the cutting action, the quartz would be induced to respond and vibrate in sympathy with the high frequency
waves and amplify the abrasive action as the tool cut through it.
The fact that there is a groove may be explained several ways. An uneven flow of energy may have caused the tool to oscillate
more on one side than the other. The tool may have been improperly mounted. A buildup of abrasive on one side of the tool
may have cut the groove as the tool spiraled into the granite.
That the hole and the core have tapered sides is perfectly normal if we consider the basic requirements for all types of cutting
tools. This requirement is that clearance be provided between the tools non-machining surfaces and the workpiece. Instead
of having a straight tube, therefore, we would have a tube with a wall thickness that gradually became thinner along its length.
The outside diameter would gradually get smaller, creating clearance between the tool and the hole, and the inside diameter
would get larger, creating clearance between the tool and the central core. This would allow a free flow of abrasive slurry to
reach the cutting area. It would also explain the tapering of the sides of the hole and the core. Since the tube-drill was a softer
material than the abrasive, the cutting edge would gradually wear away. The dimensions of the hole would correspond to the
dimensions of the tool at the cutting edge. As the tool became worn, the hole and the core would reflect this wear in the form
of a taper.
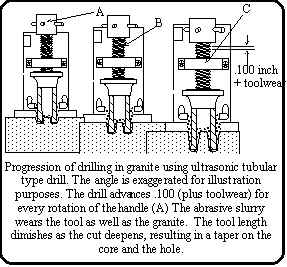
Mechanism For Ultrasonic Drilling.
The spiral groove can be explained if we consider one of the methods that is predominantly used to uniformly advance
machine components. The rotational speed of the drill is not a major factor in this cutting method. The rotation of the drill is
merely a means to advance the drill into the workpiece. Using a screw and nut method the tube drill could be efficiently
advanced into the workpiece by turning the handles (A) in a clockwise direction. The screw (B) would gradually thread
through the nut (C), forcing the oscillating drill into the granite. It would be the ultrasonically induced motion of the drill that
would do the cutting and not the rotation. The latter would only be needed to sustain a cutting action at the workface. By
definition, therefore, the process is not a drilling process, by conventional standards, but a grinding process, in which abrasives
are caused to impact the material in such a way that a controlled amount of material is removed.
The theory of ultrasonic machining resolves all the unanswered questions where other theories have fallen short. Methods may
be proposed that might cover a singular aspect of the machine marks and not progress to the method described here. It is
when we search for a single method that provides an answer for all the data that we move away from primitive and even
conventional machining and are forced to consider methods that are somewhat anomalous for that period in history.
On February 22, 1995 at 9 A.M. I had my first experience of being on camera. It was interesting, and not at all what I
expected. I was standing in the central "Kings Chamber" of the only remaining wonder of the world, the Great Pyramid.
Graham Hancock and Robert Bauvall breezed patiently through the script with me, like old pros, while I fumbled with
instructions barked at me by Roel Oostra, the producer from Netherlands Television. In a few sound bites, I had to convey to
an audience that there was something more to the sarcophagus, a large red granite box which resides inside the chamber, than
is evident to the lay-person or casual observer.
I was invited there by Robert Bauvall (The Orion Mystery) and Graham Hancock (Fingerprints of the Gods) to participate in
a documentary which has been broadcast on several channels since then. While there, I came across and was able to measure
some artifacts produced by the ancient pyramid builders which prove beyond a shadow of a doubt that highly advanced and
sophisticated tools and methods were employed by this ancient civilization. Two of the artifacts in question are well known,
another is not, but it is more accessible, since it is laying out in the open partly buried in the sand of the Giza plateau.
For this trip to Egypt I had brought along some instruments with which I had planned to inspect features I had identified on my
previous trip in 1986. The instruments were:
1. A "parallel": A flat ground piece of steel about 6 inches long and 1/4 inch thick. The edges are ground flat within .0002 inch.
2. An Interapid indicator. (Known as a clock gauge by my British compatriots.)
3. A wire contour gage. A device used by die sinkers to form around shapes.
4. Hard forming wax.
I had brought along the contour gage to check the inside of the mouth of the southern shaft inside the Kings Chamber.
Unfortunately, I found out after getting there that things had changed since I was there in 1986. In 1993, a German robotics
engineer named Rudolph Gantenbrink had installed a fan inside this mouth; therefore, it was inaccessible to me and I was
unable to check it.
I had taken along the parallel for quick checking the surface of granite artifacts to determine their precision. The indicator was
to be attached to the parallel for further inspection of suitable artifacts. The indicator, didnt survive the rigors of international
travel, though, but the instruments I was left with were adequate for me to form a conclusion about the precision to which the
ancient Egyptians were working.
The first object I inspected was the sarcophagus inside the second (Khafras) pyramid on the Giza Plateau. I climbed inside
the box and, with a flashlight and the parallel, was astounded to find the surface on the inside of the box perfectly smooth and
perfectly flat. Placing the edge of the parallel against the surface I shone my flashlight behind it. No light came through the
interface. No matter where I moved the parallel, vertically, horizontally, sliding it along as one would a gage on a precision
surface plate I couldnt detect any deviation from a perfectly flat surface. A group of Spanish tourists found it extremely
interesting, too, and gathered around me as I, quite animated, exclaimed into my tape recorder, "Space-age precision!"
The tour guides, at this point, were becoming quite animated too. I sensed that they probably didnt think it was appropriate
for a live foreigner to be where they believe a dead Egyptian should go, so, I respectfully removed myself from the
sarcophagus and continued my examination on the outside. There were more features of this artifact that I wanted to inspect,
of course, but didnt have the freedom to do so. The corner radii on the inside appeared to be uniform all around with no
variation of precision of the surface to the tangency point. I was tempted to take a wax impression, but the hovering guides
with their baksheesh expectancies inhibited this activity. (I was on a very tight budget.)
My mind was racing as I lowered myself into the narrow confines of the entrance shaft and climbed to the outside. The inside
of a huge granite box finished off to a precision that we reserve for precision surface plates? How did they do this? And why
did they do it? Why did they find this piece so important that they would go to such trouble? It would be impossible to do this
kind of work on the inside of an object by hand. Even with modern machinery it would be a very difficult and complicated
task!
Petrie gave the dimensions of this coffer, in inches, as - outside, length 103.68, width 41.97, height 38.12; inside, length
84.73, width 26.69, depth 29.59. He stated that the mean variation of the piece was .04 inch. Not knowing where the
variation he measured was, Im not going to make any strong assertions except to say that its possible to have an object with
geometry that varies in length, width and height and still maintain perfectly flat surfaces. Surface plates are ground and lapped
to within .0001-0003 inch depending on the grade of surface plate you buy. The thickness of them, though, may vary more
than the .04 inch that Petrie noted on this sarcophagus.
A surface plate, though, is a single surface and would represent only one outside surface of a box. Not only that, the
equipment used to finish the inside of a box would be vastly different than that used to finish the outside. The task would be
much more problematic. I was constructing in my mind the equipment I would need to grind and lap the inside of a box to the
accuracy I had witnessed and produce a precise and flat surface to the point where the flat surface meets the corner radius.
There are physical and technical problems associated with a task like this that are not easy to solve. One could use drills to
rough the inside out, but when it came to finishing a box of this size with an inside depth of 29.59 inches, and maintain a corner
radius of less than 1/2 inch. There are some significant challenges to overcome.
While being extremely impressed with this artifact, I was even more impressed with other artifacts found at another site in the
rock tunnels at the temple of Serapeum at Saqqarra, the site of the step pyramid and Zosers tomb.
I had followed Graham and Robert on their trip to this site for a filming on Feb. 24, 1995. We were in the stifling atmosphere
of the tunnels, where dust kicked up from tourists lay heavily in the still air. These tunnels contain 21 huge granite boxes. Each
box weighs an estimated 65 tons, and, together with the huge lid that sits on top of them, the total weight of the assembly is
around 100 tons. Just inside the entrance of the tunnels there is a lid that had not been finished and beyond this lid, barely
fitting within the confines of one of the tunnels, is a granite box that had also been rough hewn.
The granite boxes are 13 ft. long, 7 1/2 ft. wide and 11 ft. high. They are installed in "crypts" that were hewn out of the
limestone bedrock at staggered intervals along the tunnels. The floors of the crypts were about 4 ft. below the tunnel floor, and
the boxes were set into a recess in the center. Robert Bauvall was addressing the engineering aspects of installing such huge
boxes within a confined space where the last crypt was located near the end of the tunnel; a dead end with no room for the
hundreds of slaves pulling on ropes, according to theories proposed by those who believe that the ancient pyramid builders
were a primitive society.
While Graham and Robert were filming, I jumped down into a crypt and placed my parallel against the outside surface of the
box. It was perfectly flat. I shone the flashlight and found no deviation from a perfectly flat surface. I clambered through a
broken out edge into the inside of another giant box and again, I was astonished to find it astoundedly flat. I looked for errors
and couldnt find any. I wished at that time that I had the proper equipment to scan the entire surface and ascertain the full
scope of the work. Nonetheless, I was perfectly happy to use my flashlight and straight edge and stand in awe of this
incredibly precise and incredibly huge artifact. Checking the lid and the surface on which it sat, I found them both to be
perfectly flat. It occurred to me that this gave the manufacturers of this piece a perfect seal. Two perfectly flat surfaces
pressed together, with the weight of one pushing out the air between the two surfaces! The technical difficulties in finishing the
inside of this piece made the sarcophagus in Khafras pyramid seem like a walk in the park.
I was accompanied by Canadian researcher Robert McKenty at this time. He saw the significance of the discovery and was
filming with his camera. At that moment I knew how Howard Carter must have felt when he discovered Tutenkahmens tomb.
I yelled for Graham and Robert to share the discovery, but was denied their presence by Roel Oostra, who was working to a
tight schedule and had to complete his filming.
The dust filled atmosphere in the tunnels was extremely unhealthy. I could only imagine what it would be like if I was finishing
off a piece of granite, regardless of what method I used, how unhealthy it would be. Surely it would have been better to finish
the work in the open air? I was so astonished by this find that it didnt occur to me until later that the builders of these relics,
for some esoteric reason, intended for them to be ultra precise. They had taken the trouble to bring into the tunnel the
unfinished product and finish it underground for a good reason! It is the logical thing to do if you require a high degree of
precision in the piece that you are working. To finish it with such precision at a site that maintained a different atmosphere and
a different temperature, such as in the open under the hot sun, would mean that when it was finally installed in the cool,
cave-like temperatures of the tunnel, you would lose that precision. The granite would change its shape, or creep. The
solution, of course, was to prepare the precision surfaces in the location in which they were going to be housed.
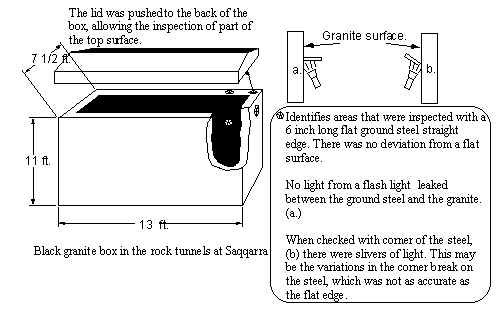
This discovery, and the realization of its critical importance to the artisans that built it, went beyond my wildest dreams of
discoveries to be made in Egypt. For a man of my inclination, this was better than King Tuts tomb.
The Egyptians intentions with respect to precision is perfectly clear. But for what purpose? In America today, the cost of just
the quarried granite would be $115,000.00. Thats without shipping costs and manufacturing costs, assuming there was
equipment available to machine it. I have contacted four precision granite manufacturers in the US and havent been able to
find one who can do this kind of work.
These artifacts need to be thoroughly mapped and inspected with the following tools.
1. A laser interferometer with surface flatness checking capabilities
2. An ultrasonic thickness gage to check the thickness of the walls to determine their consistency to uniform thickness.
3. An optical flat with monochromatic light source. Are the surfaces really finished to optical precision?
With Eric Leither of Tru-Stone Corp, I discussed in a letter the technical feasibility of creating several Egyptian artifacts,
including the giant granite boxes found in the bedrock tunnels the temple of Serapeum at Saqqarra. He responded as follows.
"Dear Christopher,
First I would like to thank you for providing me with all the fascinating information. Most people never get the
opportunity to take part in something like this.
You mentioned to me that the box was derived from one solid block of granite. A piece of granite of that size is
estimated to weigh 200,000 pounds if it was Sierra White granite which weighs approximately 175 lb. per cubic foot.
If a piece of that size was available, the cost would be enormous. Just the raw piece of rock would cost somewhere in
the area of $115,000.00. This price does not include cutting the block to size or any freight charges.
The next obvious problem would be the transportation. There would be many special permits issued by the D.O.T.
and would cost thousands of dollars. From the information that I gathered from your fax, the Egyptians moved this
piece of granite nearly 500 miles. That is an incredible achievement for a society that existed hundreds of years
ago.."
Eric went on to say that his company did not have the equipment or capabilities to produce the boxes in this manner. He said
that his company would create the boxes in 5 pieces, ship them to the customer, and bolt them together on site.
The final artifact I inspected was a piece of granite I quite literally stumbled across while strolling around the Giza Plateau later
that day. I concluded, after doing a preliminary check of this piece, that the ancient pyramid builders had to have used a
three-axes machine to guide the tool that created it. Outside of being incredibly precise, normal flat surfaces, being simple
geometry, can justifiably be explained away by simple methods. This piece, though, drives us beyond the question normally
pondered - "what tools were used to cut it?" - to a more far reaching question.. - "what guided the cutting tool?"
In answering this question, and being comfortable with the answer, it is helpful to have a working knowledge of contour
machining.
Many of the artifacts that modern civilization produces would be impossible to produce using simple hand work. We are
surrounded by artifacts that are the result of men and women employing their minds to create tools which overcome their
physical limitations. We have developed machine tools to create the dies that produce the aesthetic contours on the cars that
we drive, the radios we listen to and the appliances we use.
To create the dies to produce these items, a cutting tool has to accurately and consistently follow a predetermined contoured
path in three dimensions. In some applications it will move in three dimensions, simultaneously using three or more axes of
movement. The artifact that I was looking at required a minimum of three axes to machine it. When the machine tool industry
was relatively young, techniques were employed where the final shape was finished by hand, using templates as a guide.
Today, with the use of precision computer numerical control machines, there is little call for hand work. A little polishing to
remove unwanted tool marks may be the only hand work required. To know that a piece has been produced on such a
machine, therefore, one would expect to see a precise surface with indications of tool marks that show the path of the tool.
This is what I found on the Giza Plateau, laying out in the open south of the Great Pyramid about 100 yards east of the second
pyramid.
There are so many rocks of all shapes and sizes lying around this area to the untrained eye, this one could easily be
overlooked. To a trained eye, it may attract some cursory attention and a brief muse. I was fortunate that it both caught my
attention, and that I had the tools with which to inspect it.
There were two pieces laying close together, one larger than the other. They had originally been one piece and had been
broken. With the exception of my broken indicator gage, I found I needed every tool that I had brought with me to inspect it.
In inspecting this piece, I was interested in the accuracy of the contour and its symmetry.
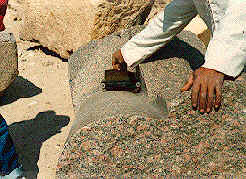
Contoured Block of Granite - Giza
What we have is an object that, three dimensionally as one piece, could be likened to a small sofa. The seat is a contour that
blends into the walls of the arms and the back. The contour was checked using the profile gage along three axes of its length,
starting at the blend radius near the back, and ending near the tangency point, which blended smoothly where the contour
radius meets the front. The wire radius gage is not the best way to determine the accuracy of this piece. When adjusting the
wires at one position on the block and moving to another position, the gage could be re-seated on the contour, but questions
could be raised as to whether the hand that positioned it compensated for some inaccuracy in the contour. However, placing
the parallel at several points along and around the axes of the contour, I found the surface to be extremely precise. At one
point near a crack in the piece, there was light showing through, but the rest of the piece allowed very little to show.
During this time, I had attracted quite a crowd. Its difficult to traverse the Giza Plateau at the best of times without getting
attention from the camel drivers, the donkey riders and the purveyors of trinkets. It wasnt long after I had pulled the tools out
of my back-pack that I had two willing helpers, Mohammed and Mustapha, who werent at all interested in compensation. At
least thats what they told me. But I can honestly say that I lost my shirt on that adventure. I had cleaned sand and dirt out of
the corner of the larger block and washed it out with water. I used a white T-shirt that I was carrying in my back-pack to
wipe the corner out so I could get an impression of it with forming wax. Mustapha, talked me into giving him the shirt before I
left. I was so inspired by what I had found I tossed it to him.
Mohammed held the wire gage at different points along the contour while I took photographs of it. I then took the forming
wax and heated it with a match, kindly provided by the Movenpick hotel, then pressed it into the corner blend radius. I then shaved off the splayed part and positioned it at different points around. Mohammed held the wax still
while I took photographs. By this time there was an old camel driver and a policeman on a horse looking on.
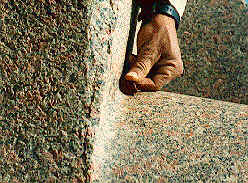
Location where the wax impression was taken.
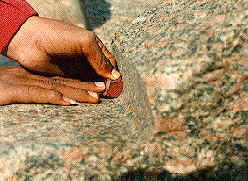
Verifying the radius at another location
What I discovered with the wax was a uniform radius, tangential with the contour and the back and side walls. Returning to
the US, I measured the wax and found, using a radius gage, that it was a true radius and measured 7/16 inch.
The side arm blend radius has a design feature that is common engineering practice today. By cutting a relief at the corner, a
mating part that is to match, or butt up against the surface with the large blend radius, may have a smaller radius. This feature
provides for a more efficient operation because it allows a cutting tool with a large diameter, and, therefore, a large radius, to
be used. With greater rigidity in the tool, more material can be removed when taking a cut.
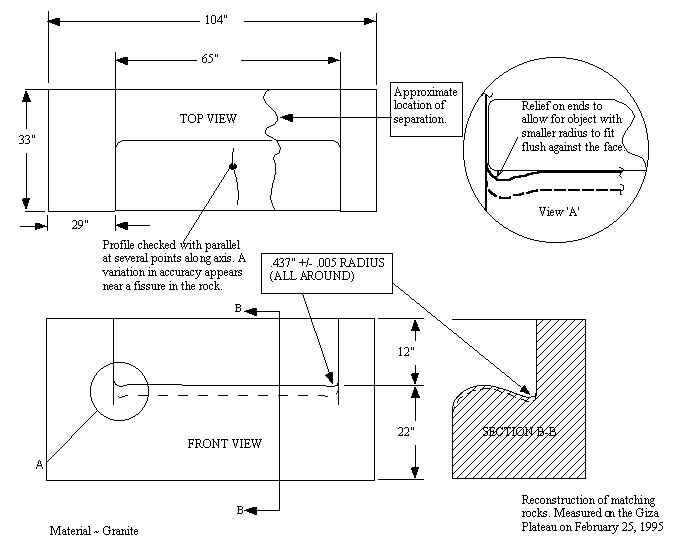
I believe there is more, much more, that can be gleaned using these methods of study. The Cairo Museum contains many
artifacts that will reveal much the same conclusion that Im presenting in this paper. In terms of a more thorough understanding
of the level of technology employed by the ancient pyramid builders, the implications of these discoveries are tremendous. We
are not only presented with hard evidence that seems to have eluded us for decades and which provides further evidence
proving the ancients to be advanced, we are also provided with an opportunity to re-analyze everything with a different
perspective, from a different angle. Understanding how something is made opens up a different dimension when trying to
determine why it was made.
The precision in these artifacts is irrefutable. Even if we ignore the question of how they were produced, we are still faced with
the question of why such precision was needed. The implications of this question are just as profound.
Revelation of new data, invariably spawns new questions. In this case its understandable to hear, "where are the machines?"
Machines are tools. The question should be applied universally and can be asked of anyone who believes other methods may
have been used. The fact of the matter is that tools have not been found to explain any theory! More than eighty pyramids
have been discovered in Egypt, and the tools that built them have never been found. Even if we mis-guidedly accept the notion
that copper tools are capable of producing these incredible artifacts, the few copper implements that have been uncovered do
not represent the number of such tools that would have been used if every stonemason who worked on the pyramids at just
the Giza site owned one. In the Great Pyramid alone, there are an estimated 2,300,000 blocks of stone, both limestone and
granite, weighing between 2½ tons and 70 tons each. That is a mountain of evidence with no tools surviving to explain its
creation.
The principle of "Occams Razor", where the simplest means of manufacturing hold force until proven inadequate, has held
force over the pyramid builders methods, except there is one component of this principle that has been lacking. If the simplest
methods do not satisfy the evidence, other less simple methods are considered, and so on and so forth. There is little doubt
that the capabilities of the ancient pyramid builders have been seriously underestimated. The most distinct evidence that I can
relate is the precision and mastery of machining technologies that are only now beginning to be re-invented. Some technologies
the Egyptians possessed still astound modern artisans and engineers primarily for this reason.
The development of machine tools has been intrinsically linked with the availability of consumer goods and the desire to find a
customer. One reference point for judging a civilization to be advanced has been our current state of manufacturing evolution.
Manufacturing is the manifestation of all scientific and engineering effort. For over a hundred years this epoch has progressed
exponentially. Since Petrie first made his critical observations between 1880 and 1882, our civilization has leapt forward at
breathtaking speed to provide the consumer with goods, all created by artisans, and still, over a hundred years after Petrie,
these artisans are utterly astounded by the achievements of the ancient pyramid builders. They are astounded not so much by
comparing their own accomplishments with what they perceive a primitive society is capable of, but by comparing these
prehistoric artifacts with their own current level of expertise and technological advancement.
The interpretation and understanding of a civilizations level of technology cannot and should not hinge on the preservation of a
written record for every technique that they had developed. The "nuts and bolts" of our society do not always make good
copy, and a stone mural will more than likely be cut to convey an ideological message rather than the technique used to
inscribe it. Records of the technology developed by our modern civilization rest in media that is vulnerable and could
conceivably cease to exist in the event of a world wide catastrophe, such as a nuclear war or another ice age. Consequently,
after several thousand years, an interpretation of an artisans methods may be more accurate than an interpretation of his
language. The language of science and technology doesnt have the same freedom as speech. So even though the tools and
machines have not survived the thousands of years since their use, we have to assume, by objective analysis of the evidence,
that they did exist.
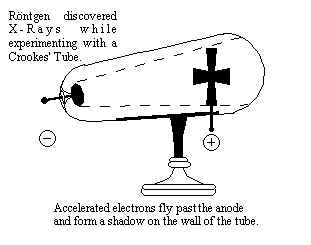
Crookes Tube.
Notwithstanding the previous argument, the ancient Egyptians did cut a mural that, while it could be interpreted as presenting a
symbolic message, also describes a technology that was being used by the contemporaries of the masons that carved it.
Inscribed into the wall in the lower crypt at the temple of Hathor at Dendera is the representation of a machine.
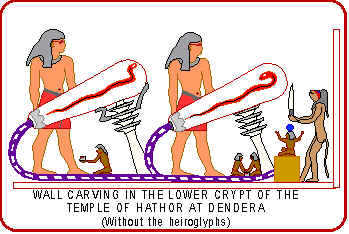
Go to Dendera to view a representation of a Crookes Tube! (Cathode Ray Tube.) Its not something you would use to cut
granite, but viewed within the context of modern scientific discovery, the Crookes tube is known as the device that triggered
the discovery of x-rays. The sketch seems to symbolize the medical profession. Put the two snakes together and Caduceus
comes to life, with representations of medicine and the proffering of the scalpel. (Symbolizing the subjugation of exploratory
surgery to the power of new technology, the x-ray?) Machines did exist. Of the kind that are in existence today, and even
those we have yet to develop.
There is much to be learned from our distant ancestors, but before that lesson will come to us, we need to open our minds and
accept that there have existed on the earth, civilizations with technology that, while different from our own, and in some areas
possibly not as advanced, had developed some manufacturing techniques that are as great or even greater. As we assimilate
new data and new views of old data, it is wise to heed the advice Petrie gave to an American who had visited him during his
research at Giza. The American expressed a feeling that he had been to a funeral after hearing Petries findings, which had
evidently shattered some favorite pyramid theory at that time. Petrie says, "By all means let the old theories have a decent
burial; though we should take care that in our haste none of the wounded ones are buried alive."
Chris Dunn can be contacted by email at: cdunn1546@aol.com
|